STL - Required file for 3D printing.
작성자
MERAIN
작성일
21-11-08 09:55
조회수
1,981
본문
RP(RPM, Rapid Prototyping) The connection with the system.
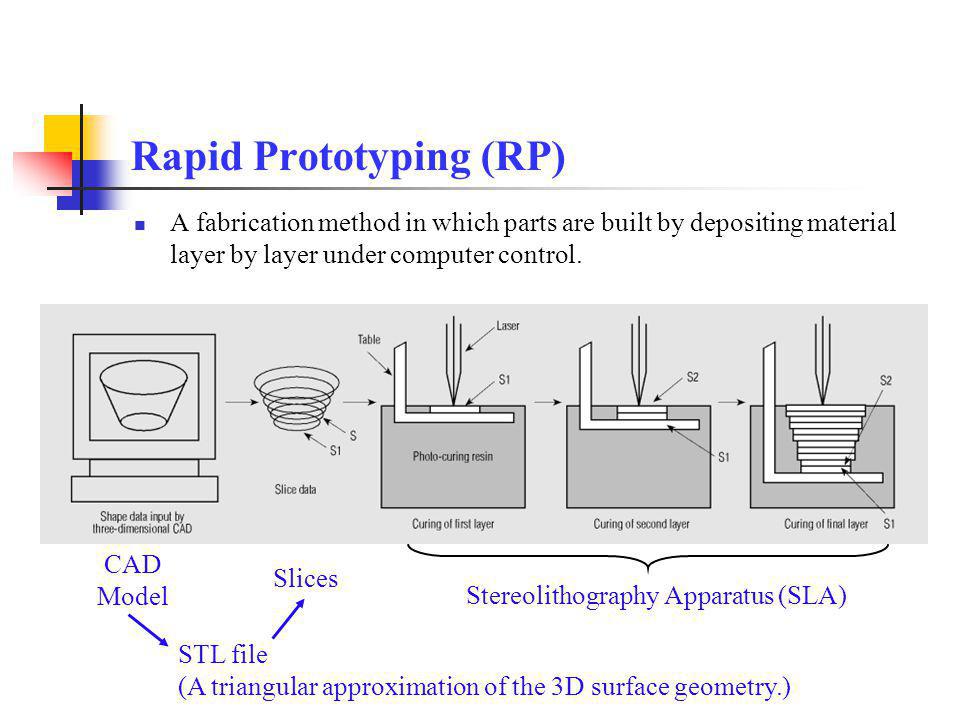
Rapid Prototyping (RPM) is a generic term for processing technology that combines CAD/CAM, cutting 3D CAD data into thin thickness to obtain a two-dimensional cross-sectional shape, and then manufacturing prototypes at high speed by a Layer by Layer method.
Many people are familiar with the term 3D printing now, but Rapid Prototyping (RP) is a processing technology that has been used for a long time.
In general, the linkage between CAD and RP (Rapid Prototyping) systems begins with the conversion of solid or surface modeling data.
STL Precautions for conversion. Precautions for conversion.
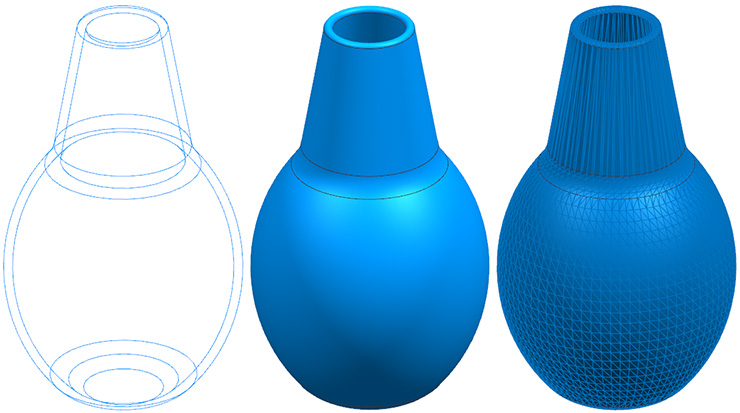
The STL file format is small triangles that access the faces of the model to contain only external information.
When converting curved and complex solid or surface models into STL files, they are converted into tens of thousands of triangles depending on the tolerance applied when converting.
* No. 1 is solid data, and No. 2 is larger in size and the triangle becomes smaller as it goes to No. 4, but it becomes more precise.
* As the number of triangles increases, it becomes more precise, but it can be seen that the capacity increases.
As the number of triangles increases, the amount of data in the STL file becomes very large. In the case of complex shapes, errors occur during the conversion process because triangles are forcibly connected and converted. To reduce this error, you need to know what information STL consists of.
- STL
3D data, which is the standard for data exchange for rapid prototyping (RP) systems, has a triangular or square minimum unit that constitutes a 3D shape, which is called a mesh. However, in STL 3D data, the minimum unit that constitutes a shape is always a triangle, which is called a facet. STL consists of numerous facets that constitute a 3D shape and has information on each facet.
The facet consists of a normal direction with a triangular plane with a vertex. In order to form an error-free STL format, the facets constituting the object must satisfy the right-hand law and the Vertex-to-Vertex rule.
STL data should always be directed outward (outside) in the normal direction.
The vertices of all facets must be connected to the vertices of neighboring facets.
The more complex the shape is, the more errors occur in the STL conversion process.
Error is...
1. When the normal vector is reversed,
2. When the facet data is off,
3. If the facet data overlaps or falls,
SW Tools to correct these STL errors also range from free to paid.
(You can see information about STL Repair tools in the link below. In Korea, the expression Fixing is used rather than Repair, but both have the same meaning.)
STL REPAIR BEST SOFTWARE TOOLS TO REPAIR STL FILES
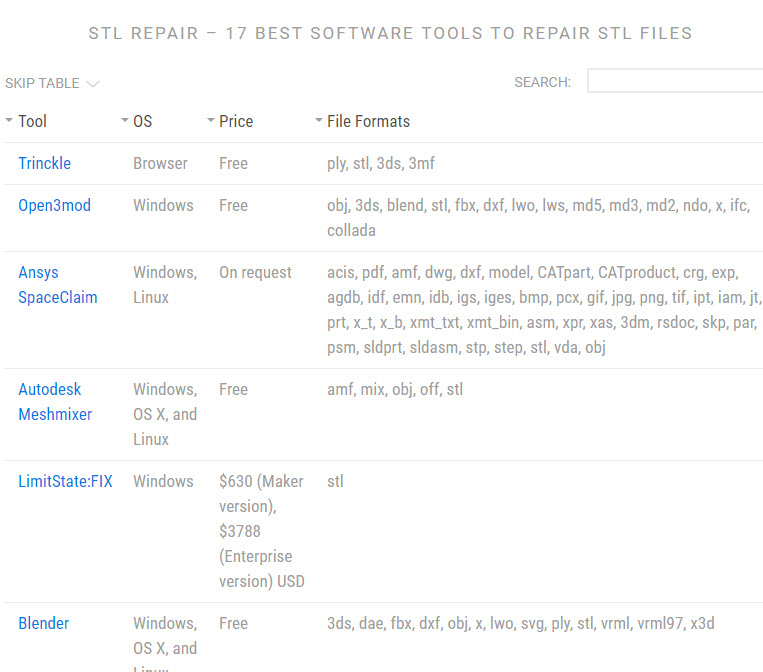
In general, STL errors cannot be prevented 100% when converting 3D data, but most 3D printing software has the ability to correct errors.
- 이전글File format covered by Magics #01 Magics 21.11.08
- 다음글Design guidelines for Direct Metal Laser melting 21.11.08