말 편자 금속 3D프린팅
작성자
MERAIN
작성일
21-11-05 14:33
조회수
2,553
본문
1) 금속3D프린팅으로 말 편자를 제작한다면 뭐가 좋을까?
편자는 말발굽의 마모를 방지하고 발굽에 발생할 수 있는 여러 가지 질병을 예방하기 위한 유효한 장치물입니다. 앞서 설명한대로 전통적으로 편자는 철로 만들어 졌으나 야금학이 발달하면서 말의 주력 종목에 맞추어서 다양한 금속으로 만들게 되었습니다.
폴로와 같은 급격한 방향 전환을 하고 격렬하게 땅을 밟아야하는 종목에는 내구성이 높은 강철을, 속도가 가장 중요한 경마에는 알루미늄을 사용합니다. 무게를 줄이면서 강도를 높이기 위하여 티타늄을 사용하기도 합니다. (해외)
경마에서 사용되는 알루미늄은 가벼운 장점이 있으나 강도가 약하여 매 월 교체 시기가 되기 전에 마모되어 장제에 많은 문제점을 안고 있습니다. 이러한 문제의 해결 방안으로 스틸에 비하여 강도는 2.2 배 높으나 비중은 2배 낮은 티타늄을 이용한 말발굽 편자를 개발하여 교체주기를 정상화하고 스캐닝을 통한 맞춤형 편자를 사용하여 그동안 당금 질로 발굽에 맞추었던 공정을 개선하여 말발굽에 딱 맞는 편자를 만들어보고자 합니다. 더불어 말발굽에 발생하는 여러 가지 질병 치료에 사용되는 치료용 편자의 사용에도 편리한 티타늄편자를 사용하기 위한 개발의 필요성이 있다고 볼 수 있습니다.
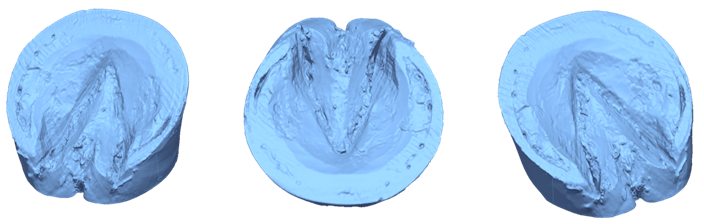
하지만 피해갈 수 없는 문제가 바로 비용이죠. 실제 제작과정에서는 제작자체의 비용보다 가장 문제가 되는 부분이 바로 설계 부분 이었습니다. 맞춤형이기 때문에 스캐닝과정을 통한 데이터를 획득하고 그에 맞춰 설계를 해야 하는 것이죠.
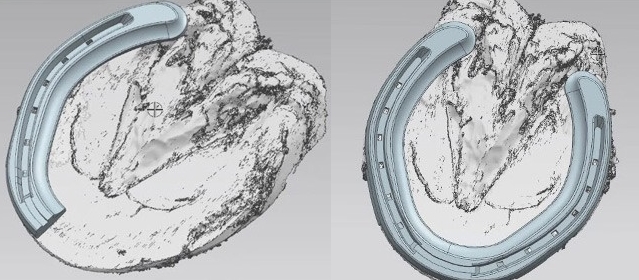
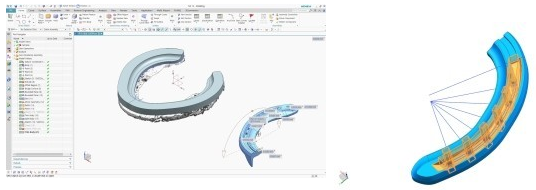
3D프린팅은 3D데이터가 없이는 제작이 불가능하기 때문입니다. 모델링에 대해 어느정도 이해와 숙련이 되어 있다고 해도 말 발굽 4족에 해당하는 모델링 데이터를 4개 제작해야 하기때문에 쉬운 작업이 아닙니다. 모델링 작업은 인건비와 직결되는 문제이기 때문에 교체주기가 빠른 편자를 매번 3D프린팅 하기가 현실적으로 어렵다고 봐야 합니다.
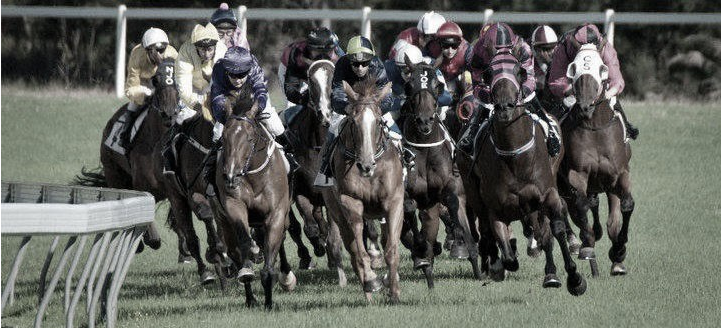
하지만 경주용말 전용 맞춤형 편자라면 얘기가좀 다르지 않을까 합니다. 게다가 알미늄보다 강도가 높은 티타늄이라면? 이제부턴 비용 문제가 아닌게 되는거죠. 금속3D프린팅은 바로 이런경우에 안성 맞춤입니다. 모든 분야와 모든 부품을 금속3D프린팅 할 필요없습니다. 금속3D프린팅은 맞춤형 고부가가치사업에 집중해야합니다.
2) 금속3D프린팅 말 편자 제작 예상 과정
말 발굽 스캐닝에 이어 설계 그리고 제작까지의 과정을 그려보면 크게 다음과 같습니다.
1. 발 발굽 3D스캔 (3차원 스캐너로 스캐닝)
2. 맞춤형 설계 (곡면 모델링에 적합한 NX로 진행)
3. 금속 3D프린팅 (미래인 David 2.0 금속3D프린팅)
4. 공차 검증 (공인인증시험기관을 통해 진행)
이런 과정으로 진행이 됩니다.
금속3D프린터는 한번 가동을 시작하면 중간에 멈추고 다시하기가 쉽지 않고 실패를 했을 때 시간과 비용적인 측면에서 손실이 막대합니다. 이번 편자 제작은 David 2.0으로 금속3D프린팅 중 PBF방식의 금속3D프린터를 사용했습니다. 편자를 만드는데 정밀도의 우선순위가 높지 않아 PBF타입말고 다른 금속3D프린터로 제작을 해도 될 것 같습니다.
그 다음은 공정변수 설정입니다. 소재의 종류 상태 그리고 장비의 성능, 그리고 제작 하고자하는 출력물을 고려하여 설정해야 합니다. 우선 편자는 용융점이 높은 티타늄으로 제작계획을 세웠습니다.
- Laser power - (230w)
- Laser Spot size - (80um)
- Spot size에 따른 Hatching distance - (80um)
- Layer thickness (금속 분말의 입도는 D10~D90까지 평균 40um이었다.) - (30um)
- Laser scan speed (Laser power와 비례하여 설정한다.) - (810m/s)
3) 금속3D프린팅 결과
금속3D프린팅으로 일반형 편자, 격자구조를 적용한 두 종류의 편자로 구성하여 제작 하였습니다.
격자구조는 3D캐드에서 특정부위를 잘라내고 그 부분에 Materialise 3-matic으로 격자를 구성하였습니다. 이런과정을 DfAM(Design for Additive Manufacturing)과정 중 하나라고 볼 수 있습니다. DfAM은 적층가공을 위한 설계,디자인 하는 것이라 이해하면됩니다.
4) 금속3D프린팅 편자 제작기간 및 경량화
말발굽 3차원 스캐닝 그리고 스캐닝데이터를 기반으로한 모델링 제작, 금속 3D프린팅을 거쳐 후처리까지 한 말의 4족에 해당하는 편자4개를 만드는데 들어가는 시간은 총 2일 정도 소요됩니다. 기존 공법으로 편자를 만드는데 들어가는 시간이 얼마나 걸리는지는 정확히 알지 못해 비교를 할 수 없었지만, 아마 어느정도는 기성품 형식으로 만들어져 있고 그걸 열로 가열하고 두들겨 만들지 않을까 생각합니다.
편자 4개(앞발2, 뒷발2) 총 제작 시간은 다음과 같습니다.
- 스캐닝&데이터 정리 : 1시간
- 모델링 시간 : 90분
- 격자 구조 적용 : 30분
- 개당 금속3D프린팅 : 8시간 이상 (4족일 경우 24~30시간 정도)
- 열처리 : 4시간
- 후가공 : 1시간 (주로 서포트 제거에 시간을 쓴다.)
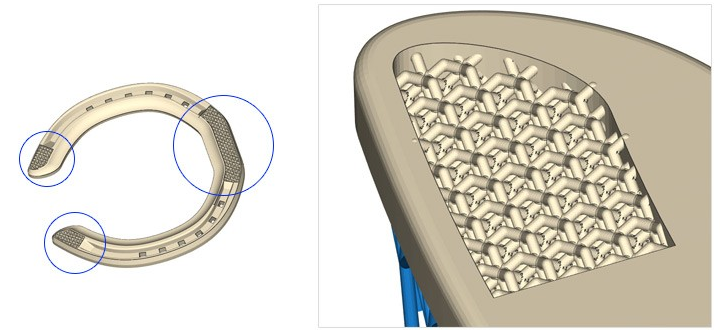
* 편자의 경우 표면처리가 필요하지 않으므로 서포트 제거정도에서 마무리를 지을 수 있습니다.
일반 쇠로 만든 말 편자의 평균무게가 300g임을 감안할때 120g으로 60%경량화가 가능하였습니다.
5) 스캐닝을 통한 정밀도 분석
대부분 공차(치수)는 0.5mm 이내입니다.
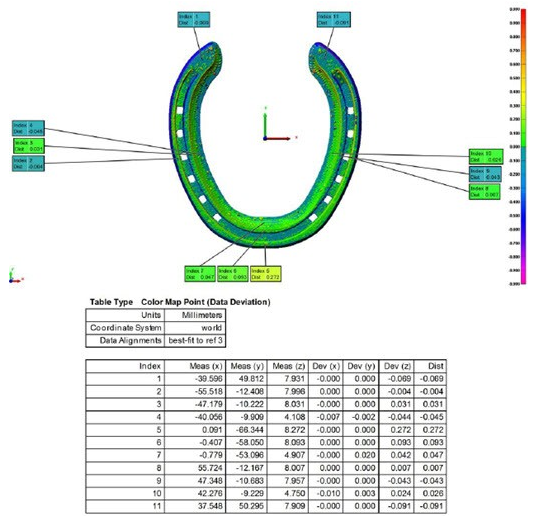
6) 금속3D프린팅 편자4개 제작비용
금속3D프린팅 출력서비스 비용을 산정하는데 필요한 근거는 모델링데이터의 크기, 부피, 소재, 플레이트의 가격을 기본으로 제작원가를 정하고 여기에 장비사용료, 열처리와 후가공 등 인건비와 자제비가 포함됩니다. 정밀하고 표면조도가 중요한 제품의 경우 후가공부분에서 비용이 많이 상승합니다. 스캐닝을 해야 하는 상황이거나 모델링을 해야 한다면 이부분은 추가 비용이 발생 합니다. 스캐닝과 모델링은 인건비 비율이 100%에 해당되어 결국 제작단가를 낮추려면 한번 제작을할 때 최대한 많은 부품을 한번에 뽑아야한다는 결론이 나옵니다.
편자4개의 경우 보통 편자1개당 초기에는 50만원정도이고 그 후 같은 제품을 지속적으로 제작한다면 아마 20~30만원이면 금속3D프린팅 비용으로 적당하지 않을까 합니다. 물론 8~16개를 한번에 제작을 하였을 경우입니다. 그리고 비싼소재를 사용할수록 가격이 비쌀거라고 생각하면 안됩니다. 프린팅 비용은 용도와 목적에 따른 후가공에서 차이가 많이 납니다.
7) 결론
말발굽에 잘 맞는것은 확인 했지만 실제 말의 보행이나 단점까지 확인하기에는 시간이 부족해 더이상 진행하지 못했습니다. 이번 제작을 통해 특수목적에 해당하는 경주용마 편자 제작은 성공적입니다. 말발굽에도 잘 부착되었고 DfAM디자인을통해 경량화를 60%이상 실현하였습니다. 모든 말의 말발굽에 금속3D프린팅을 적용할 수는 없습니다. 그리고 앞으로도 그럴일 없다고 생각하지만 금속3D프린팅 기술은 적용하고자 하는 대상과 목적 그리고 비용까지 고려하면서 진행한다면 최고의 부가가치를 가져올 수 있다고 생각합니다.
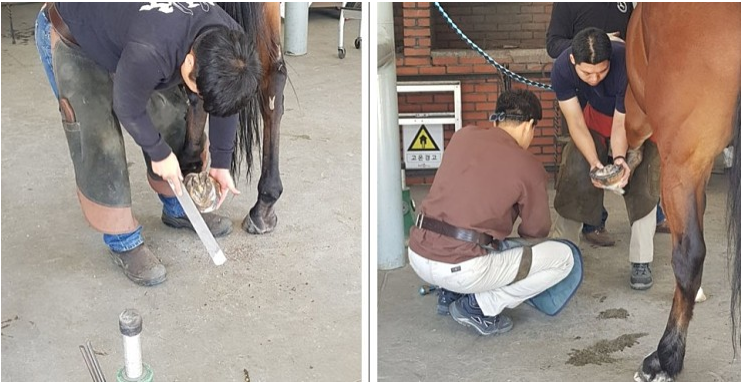
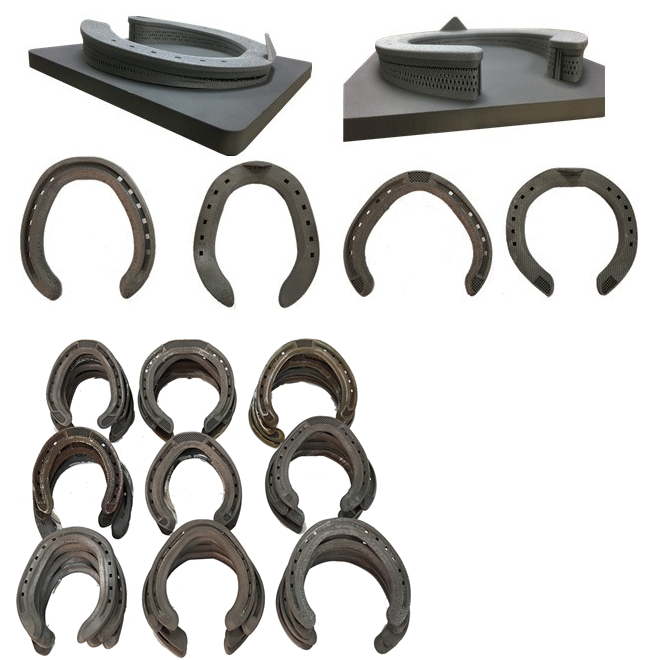
- 이전글넘침을 경계하는 잔 - 계영배 - CoCr 21.11.05